今回は、「プリント基板の製造工程」についての説明です。
目次
1.プリント基板の製造工程の大まかな流れ
プリント基板がどのような工程で作られるのかを図と併せて大まかにまとめてみました。
ここでまとめたのは多層構造(パターン層が複数ある構造)のプリント基板の製造工程です。
メーカによっては微妙に工程が異なる可能性があるので、参考に留めておいてください。
まあ、大きな違いはないはずですけどね。
1.ガーバーデータを用意する。
プリント基板を作るには、部品配置(パッドやランドの位置)情報・層ごとのパターン配置情報・シルク情報などが必要です。
これらのデータのことをガーバーデータと呼びます。
このガーバーデータをP板.comのようなプリント基板製造会社に依頼を出すときに一緒に渡します。
すると、このガーバーデータを基にしてCAMというツールで加工が可能になります。
2.プリント基板のベース材料を切り出す。
各層の基板のベースとなる材料を適切なサイズで切り出します。
基板のベースは樹脂材料に銅箔が貼り付けられたもので、これをCCL(銅張積層板)と呼びます。

内層として使用するCCLは銅箔が両面貼りになっていますが、外層として使用する場合は銅箔が片面貼りになっていることもあります。
ですが、大抵両面貼りになっています。
理由は、片面だろうが両面だろうがかかる費用はあまり変わらないからです。
なので、内層を増やす必要があるならたいして使用しないとしても両面を使用するように統一した方が結果的に安上がりなんですね。
だから層数は基本的に偶数であることが多いです。
※ 奇数が無いというわけではない。
3.内層を形成する。
銅箔を必要なパターンだけ残して取り除く下準備として、銅箔にドライフィルムを貼り付けます。
このドライフィルムはラミネートフィルムやエッチングレジストとも呼ばれます。
ドライフィルムは、感光性のあるレジスト剤がフィルム状になったものが表面に位置しています。
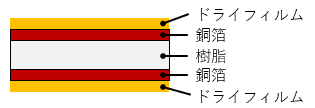
基板の回路パターンを模ったマスクを重ね合わせて、紫外線を照射します。
すると、回路パターン部分にのみ紫外線が照射され、ドライフィルムが反応して硬化(焼き付けられる)します。
この工程を露光と呼びます。
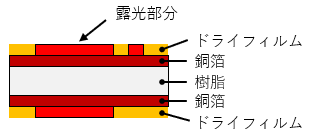
露光させた部分以外のドライフィルムは余分なので、溶融除去します。
この工程を現像と呼びます。
インスタントカメラでフィルムに焼き付けて現像するのとイメージは同じですね。
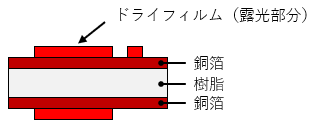
露光及び現像により、必要な回路パターン以外は銅箔が剥き出しの状態になっています。
この銅箔部分は余分なので、薬剤で溶かして除去します。
この工程をエッチングと呼びます。
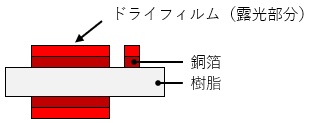
銅箔パターンの上に残っている硬化したドライフィルムはもう不要なので、除去する。

この段階で回路パターンを描いている銅箔は、表面がツルツルしていて積層時に密着しづらいです。
なので、銅箔表面を酸化処理してわざと粗くします。
この工程のことを黒化処理と呼びます。
酸化処理すると黒く変色するという単純な理由からこう呼ばれています。
4.内層基板と外層基板を積層する。
内層基板ができたので、外層基板を重ね合わせてプレス機にかけます。
この時、内層基板と外層基板の間にはプリプレグと言う接着剤を挟みます。
プリプレグは半硬化状態の樹脂で、加熱すると融けます。
融けると接着剤として機能しますので、加圧・加熱処理をしながらプリプレグが完全硬化する温度まで加熱して接着します。
内層基板が複数ある場合、間にプリプレグを入れて同じように積層して接着していきます。
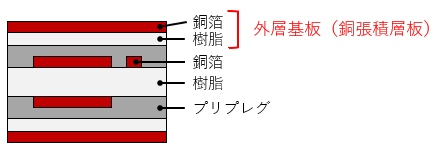
5.基板に穴を開ける。
スルーホール(部品固定穴)・ノンスルーホール(ねじ固定穴)・ビアホール(層を繋ぐための穴)などを開けます。
穴の開け方は、ドリルで層を全部まとめて貫通させる方法と、特定の層のみレーザーを使って穴開けする方法(ビルドアップ工法)があります。
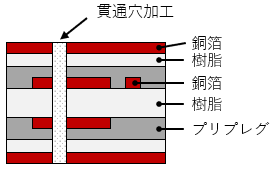
6.必要に応じて穴を銅メッキ加工する。
ノンスルーホールはねじ固定穴なのでメッキ加工は不要ですが、外層と内層を電気的に接続する必要がある穴は銅メッキ処理をします。
7.外層を形成する。
外層基板はCCLなので、「3.内層を形成する。」と同様の処理を施し、必要な銅箔パターンのみ残します。
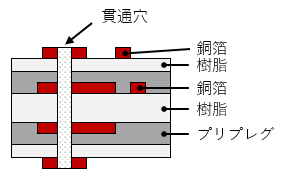
8.ソルダーレジストで絶縁する。
内層基板はプリプレグが接着剤兼絶縁体として役立っているので銅箔パターンが保護されているのですが、外層基板はこのままでは銅箔パターンが露出した状態になってしまいます。
銅箔パターンが露出していると部品実装時のはんだが飛び散ったり埃が付着することにより銅箔同士が短絡(ショート)する危険性があります。
そこで、ソルダーレジストという絶縁性(耐熱性もある)のインクを塗ります。
パッドやランドのような後ではんだ付けをする銅箔箇所は露出させておきますが、それ以外の箇所はソルダーレジストを塗りたくります。
処理方法は「3.内層を形成する。」と似ていて、ソルダーレジストを塗る(内層のドライフィルムを貼る工程)→乾燥させる(露光する)→未硬化部分を除去する(現像する)という流れになります。
残っている硬化したソルダーレジストは必要なので付けたままにするという点は内層の時と異なりますね。
ちなみに、ソルダーレジストは基本的に緑色で、プリント基板の緑はこの色だったりします。
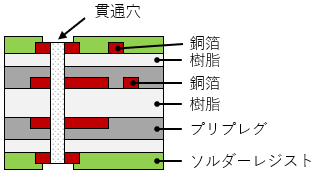
9.表面処理をする。
銅箔の露出しているパッドやランドは、そのままにしておくと空気と反応して酸化してしまいます。
なので、場合によっては銅箔の露出部表面に何かしらの処理が必要です。
一般的には水溶性プリフラックス処理を行うことが多いです。
詳しくは以下の記事にまとめていますので、説明は割愛します。
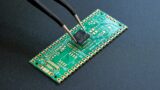
10.シルクを印刷する。
基板の型式・会社のロゴ・部品実装位置・部品実装向きなどをソルダーレジスト上に印刷します。
この印刷された文字のことをシルクと言います。
『印字じゃないの?』と思うかもしれませんが、インクジェットプリンタなどで“印刷”するのが一般的なので、この言い方が正しいです。
11.外形加工する。
ルーターを使ってプリント基板の不要な部分を切断したり、VカットというV字型の溝を入れて後で手で簡単に切り離せるように加工します。
Vカットは、部分部分が大きければ手で折り曲げて切り離せるのですが、小さいところは力が入りづらいのでラジオペンチを使うのが無難です。
曲線などを作りたい場合はミシン目も駆使する必要があります。
12.検査をする。
プリント基板を出荷する前に導通検査や外観調査を実施します。
以上がプリント基板の大まかな製造工程です。
後は納入されたPWBに各自で部品を実装すればPCBの完成です。
以上、「プリント基板の製造工程」についての説明でした。